LOV™ OIL MIST SEPARATOR
HOW TO SEPARATE LUBE OIL MIST?
THREE CASE HISTORIES FOR OIL MIST REMOVAL – TURBINE & COMPRESSOR SECTOR
AWS can contribute to the solution of many pollution control problems caused by oil mist. The lubricated rotating parts of all gas and steam turbines, turbo compressors and vacuum pumps generate a visible oil plume which is to be removed from the air vented to atmosphere. The installation of a simple but effective mist eliminator on the lube oil vent solves the pollution problem and, by recovering the expensive oil, pays off the mist eliminator cost in a short period of time. In this article you will find 3 different cases solved with AWS LOVTM mist separators.
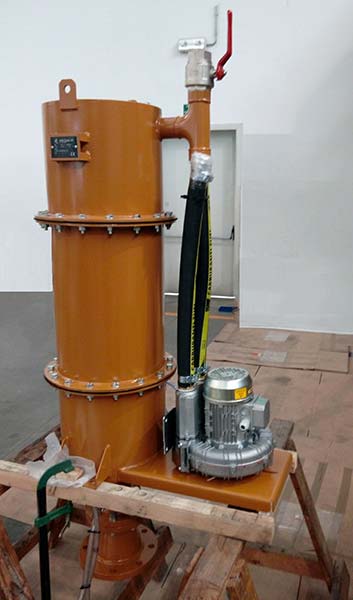
LOV LS100
- Gas flowrate: 100 Nm3/h
- Temperature: max 70 °C
Technical solution:
In this case the customer asked for Carbon steel material, finished with specific paint. The filtering media is our special glass fiber rope that does all the “dirty work” and removes the oil mist passing through the system from the gas stream.
The pressure drop across the system is less than 180 MM W.G.
As you can see, the system has a blower and several pipes, but its design is studied in order to save space and make it compact but perfectly efficient.
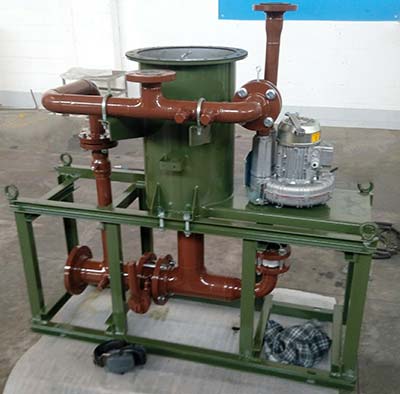
LOV LS100
- Gas flowrate: 100 Nm3/h
- Temperature: max 70 °C
Technical solution:
In this case the customer asked for Carbon steel material, finished with specific paint. The filtering media is our special glass fiber rope that does all the “dirty work” and removes the oil mist passing through the system from the gas stream.
The pressure drop across the system is less than 180 MM W.G.
As you can see, the system has a blower and several pipes, but its design is studied in order to save space and make it compact but perfectly efficient.
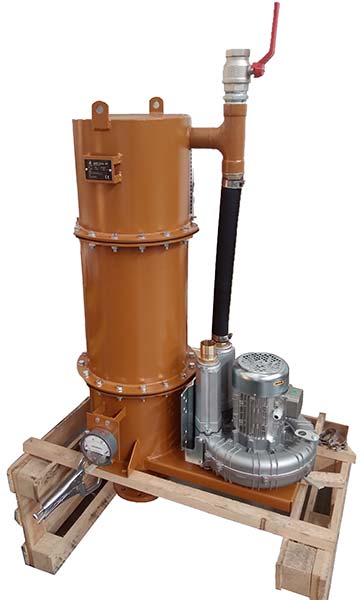
LOV LS-300
Process conditions:
- Gas flowrate: 300 Am3/h
Technical solution:
- Vessel & piping materials: painted carbon steel
- Filtering media: Special glass fiber rope
This LOVTM mist separator seems very similar to the first one, but instead there are many differences: the system is made in painted Carbon steel, stuffed with special fiber rope. The blower is much bigger than the first one because it needs to bear a much higher flowrate (300 Am3/h).
The pressure drop across the system is less than 180 MM W.G.
The only feature in common between the systems is the external shape, which can be exactly the same starting from small flowrates (50 m3/h) up to bigger flowrates (500 m3/h).